Ultrasonic rail flaw detectors from the UDS2-7X product line
Hand-pushed ultrasonic rail flaw detectors UDS2-73 and UDS2-77
The intermediate link in the railway track quality management system (in terms of ultrasonic inspection) is rail testing using hand-pushed ultrasonic trolleys, also known as single-rail and dual-rail flaw detectors. This is the most common class of equipment used on railways worldwide. Hand-pushed flaw detectors, such as the UDS2-73 and UDS2-77, are used for confirmatory inspections following high-speed ultrasonic rail testing or for primary inspections of small track sections, tight-radius curves, station tracks, and other areas where high-speed systems are impractical or ineffective.
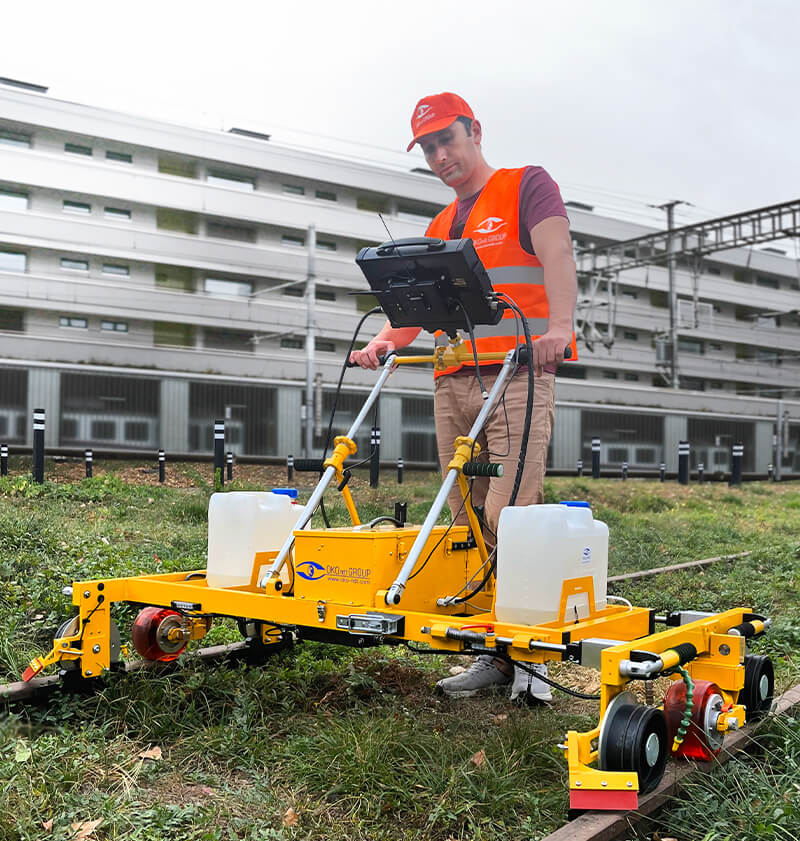
Dual-rail flaw detector UDS2-73
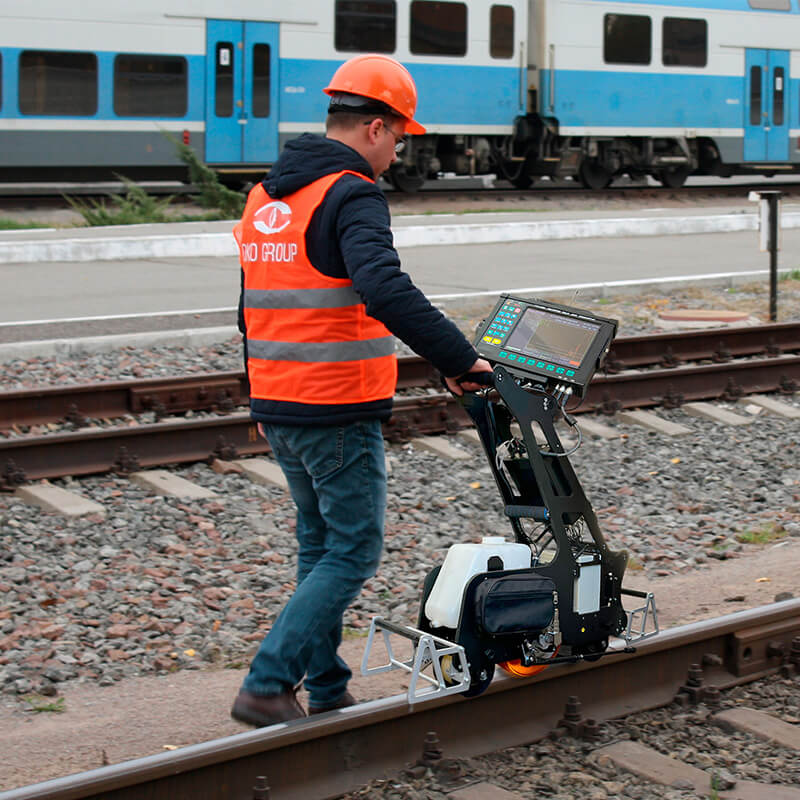
Single-rail flaw detector UDS2-77
Features of the UDS2-73 and UDS2-77 Flaw Detectors
Hand-pushed ultrasonic flaw detectors can be either single-rail or dual-rail. Single-rail models, such as the UDS2-77, are ideal for confirming individual defects, as they require only one operator, who can quickly remove the trolley from the track in case of an approaching train. Dual-rail flaw detectors, like the UDS2-73, are more convenient for continuous inspection of small track sections.
Search Systems of UDS Flaw Detectors
The UDS family flaw detectors use two types of search systems: sliding systems and wheel-type immersion systems ("ultrasonic wheels" or "wheel probes").
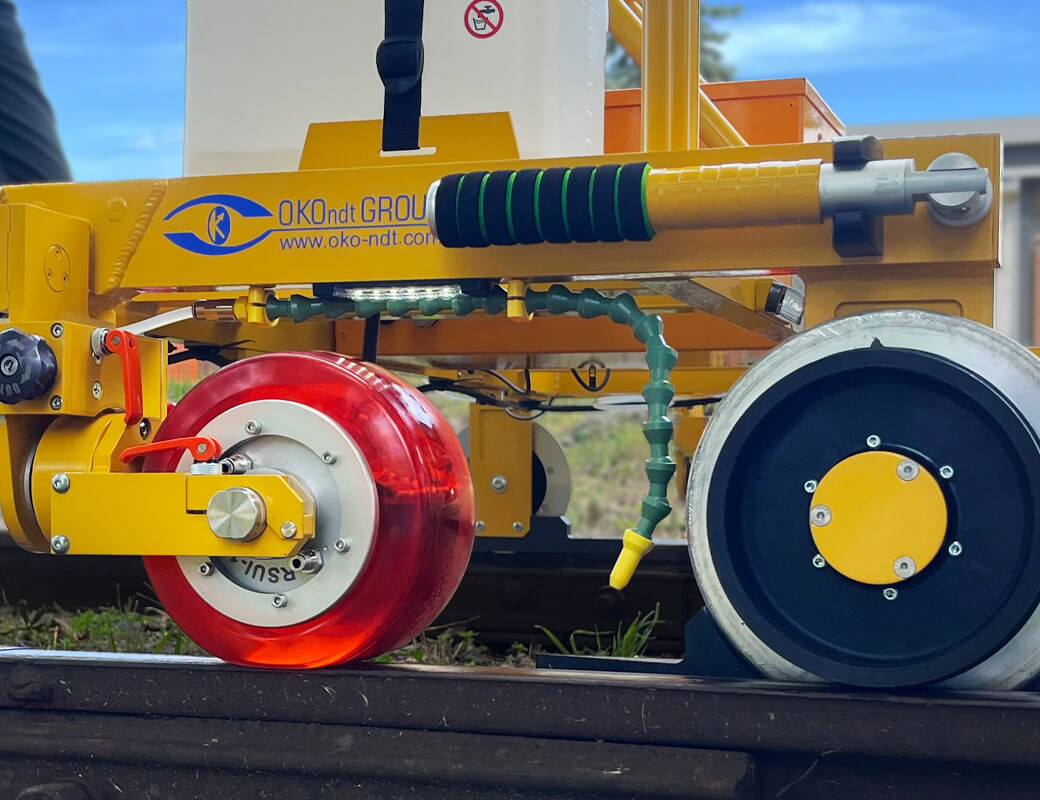
Wheel-type immersion system – the «wheel probe»
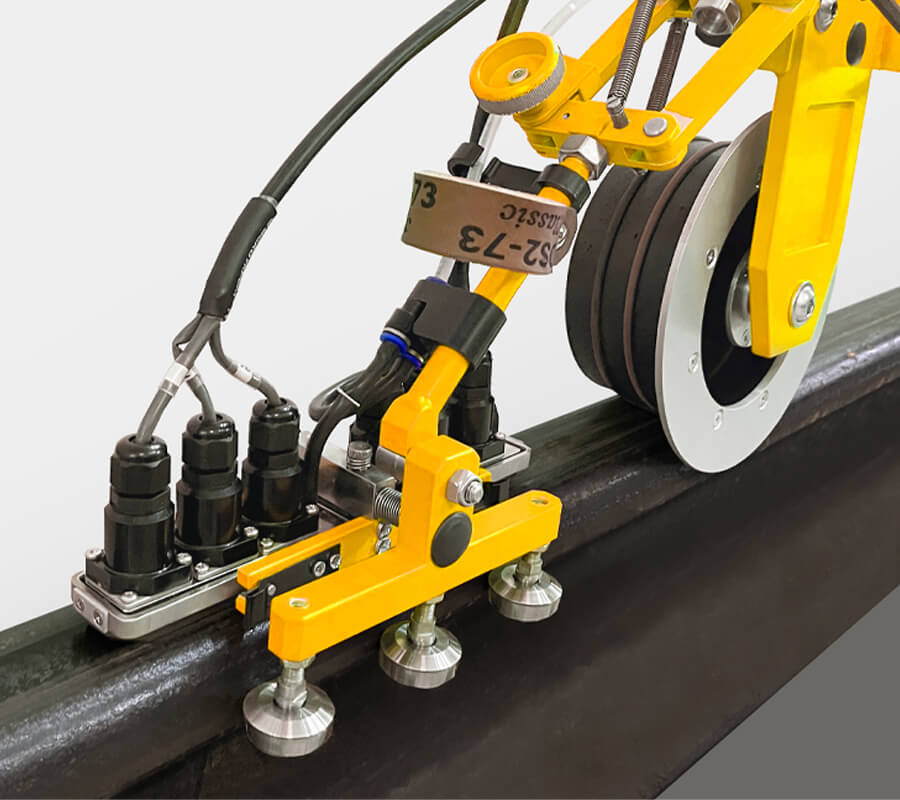
Sliding search system
Each system has its own set of advantages and disadvantages. One of the primary benefits of sliding systems is their ability to automatically position ultrasonic probes on the rail surface. This ensures consistently stable testing sensitivity, regardless of variations in the trolley's inclination. Additionally, sliding systems eliminate the need for operators to manually adjust probe angles, making them more user-friendly. However, these systems do have a downside—over time, the ultrasonic probes experience wear due to continuous contact with the rail surface, necessitating regular replacement and recalibration to maintain accurate results.
In contrast, wheel-type systems solve the issue of probe wear by enclosing the probes within a protected wheel mechanism, meaning that only the wheel tires require periodic replacement. This greatly extends the lifespan of the probes and reduces the need for regular recalibration. Nevertheless, single-rail flaw detectors that use wheel probes have a notable drawback: the unavoidable changes in trolley inclination during manual operation can cause fluctuations in sensitivity, potentially affecting the consistency of the inspection. Fortunately, this issue is significantly reduced in dual-rail flaw detectors, such as the UDS2-73 RSUI. In these models, the correct positioning of the ultrasonic wheels is configured once at the start of the inspection and then automatically maintained throughout the testing process, ensuring steady and reliable sensitivity levels.
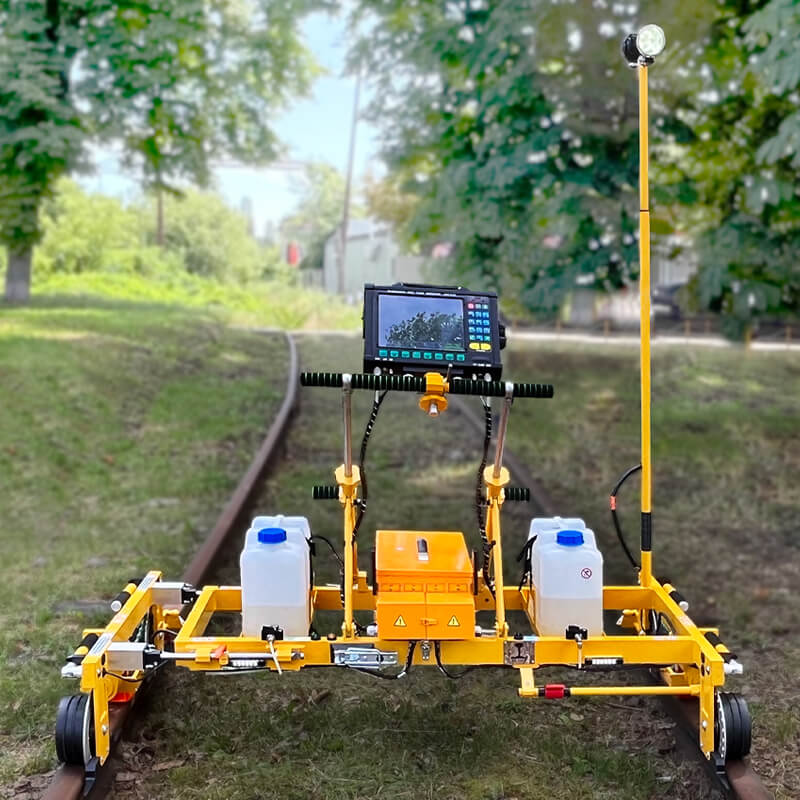
UDS2-73 RSUI inspection trolley with wheel probes and extending chassis
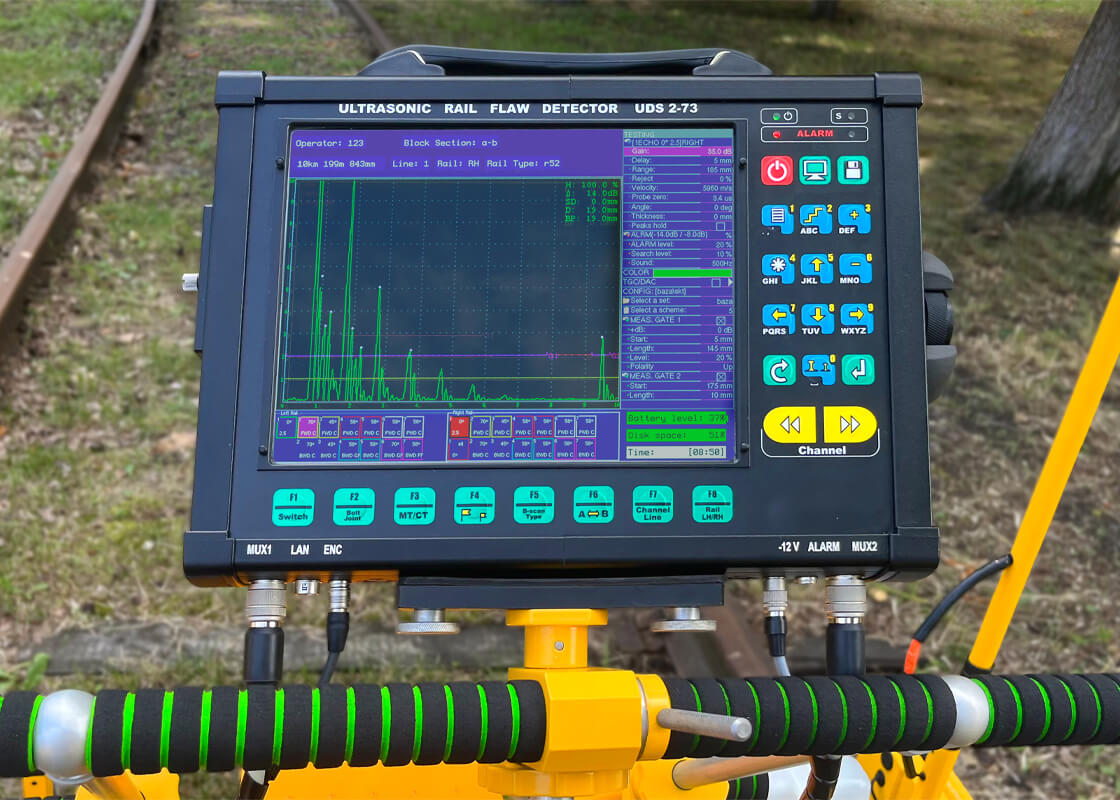
Electronic unit of the UDS2-73 RSUI
Capabilities of the UDS2-73 RSUI Flaw Detector
The UDS2-73 RSUI enables continuous ultrasonic rail inspection in compliance with standards such as EN 16729 and AREMA. It features an extending chassis for precise positioning of the ultrasonic wheels and entry bars for seamless passage through switches and frogs. The flaw detector includes a large, high-contrast 10-inch display, an intuitive interface, and an ergonomic design.
The inspection speed can reach up to 5 km/h, with a scanning step of no more than 1.5 mm along the rail path, providing high accuracy in assessing indications amplitudes. The UDS2-73 RSUI is compatible with track gauges from 950 to 1676 mm, covering all existing railway track types.
This equipment boasts IP65 protection against water and solid particles and operates within a temperature range of -30°C to +55°C, making it suitable for extreme conditions. Additionally, its probes and electronics are galvanically isolated from the rails, significantly reducing electrical interference.
Displaying Testing Results in UDS Flaw Detectors
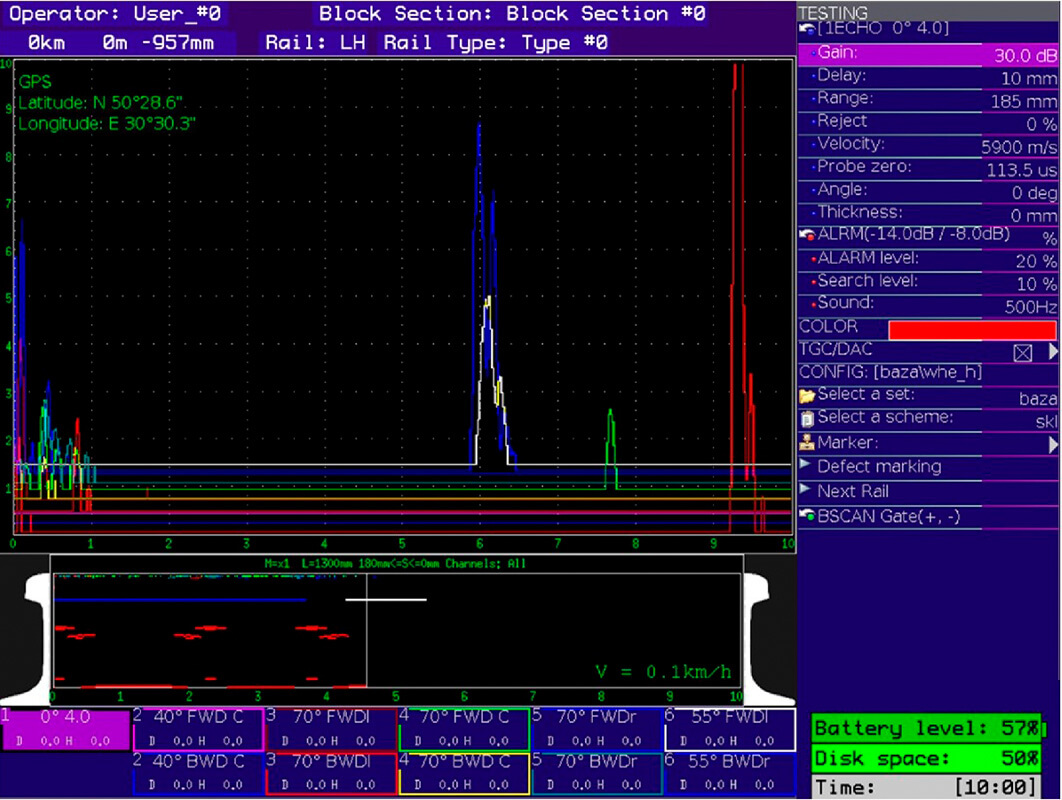
Example of inspection data representation in UDS2-73 RSUI
The flaw detector’s software allows real-time visualization of inspection results in A-Scan, multi-A-Scan, and B-Scan formats for all channels. A dedicated mode displaying the rail profile intuitively indicates defect locations. It also supports simultaneous display of B-Scans grouped by inspection zones (rail head, central projection, etc.).
During testing, operators can mark features such as "Crossing," "Bridge," and "Bolt Hole," which are saved along with the inspection data. With a built-in GPS/GNSS system, all data is recorded with both track coordinates and real-world geolocation.
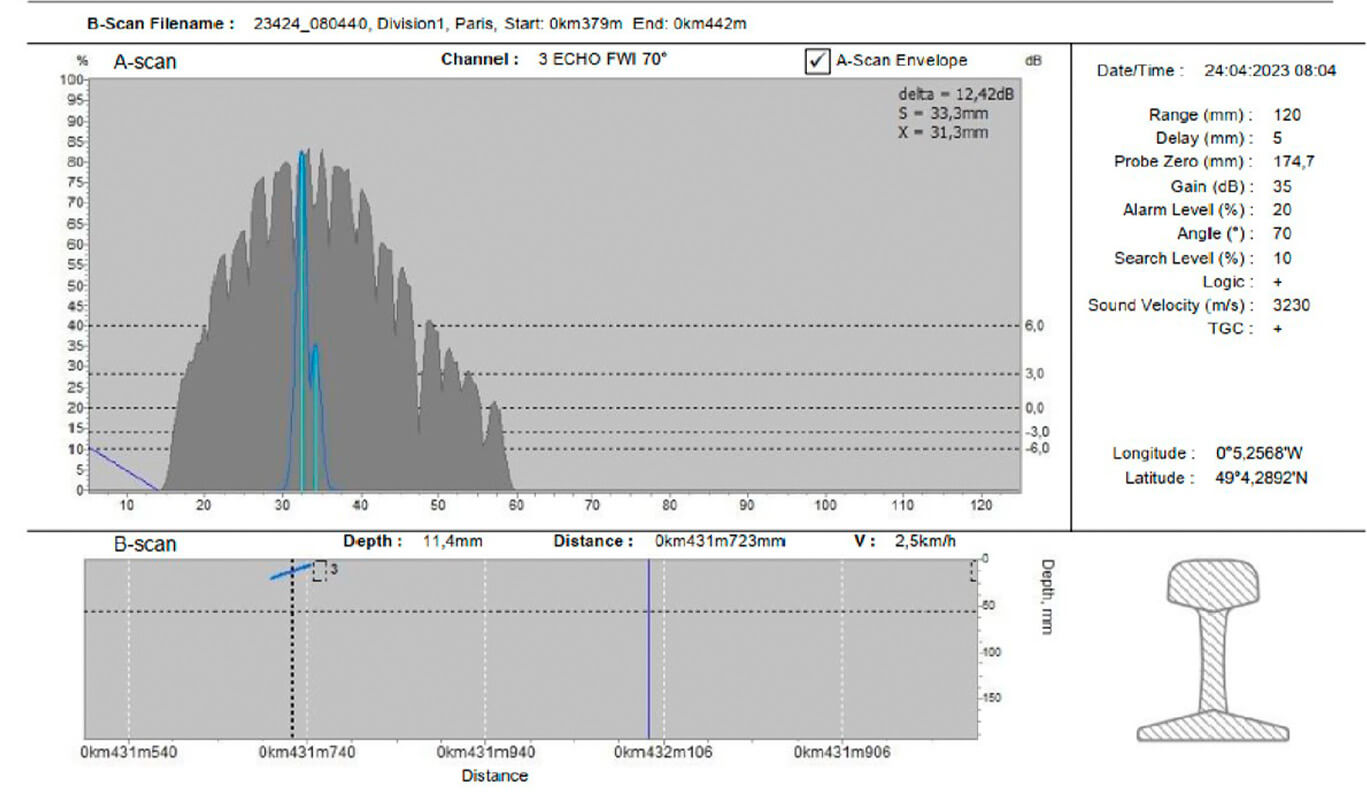
UDS2-73 RSUI Report example
Stored data can be reviewed directly on the flaw detector or transferred to a PC via a USB flash drive. The accompanying PC software offers extensive analysis and reporting capabilities allowing users to generate various types of reports, including comprehensive evaluations of individual detected defects, detailed summaries for inspected areas, and structured reports for inspection jobs conducted over a specific period of time.
Future Development of UDS PC Software
Our development team is currently working on integrating an intelligent machine analysis module into the software, which will significantly streamline the work of data analysts. This module has already proven effective in the OKOSCAN-73HS high-speed rail inspection system.